Why Regular Tank Welding Inspection is Essential for Architectural Stability
Wiki Article
The Essential Role of Container Welding Inspection in Ensuring Structural Honesty and Security Compliance in Industrial Applications
In the realm of industrial applications, tank welding examination arises as a critical element in guarding architectural integrity and ensuring conformity with security regulations. Making use of a combination of techniques such as aesthetic evaluations and progressed screening methods, these examinations serve to identify and alleviate prospective imperfections prior to they escalate right into considerable hazards. The effects of these methods extend past mere governing adherence; they fundamentally influence operational performance and asset long life. The complexities surrounding the examination process motivate a closer examination of its methods and end results, revealing layers of value that merit additional expedition.Importance of Tank Welding Inspection
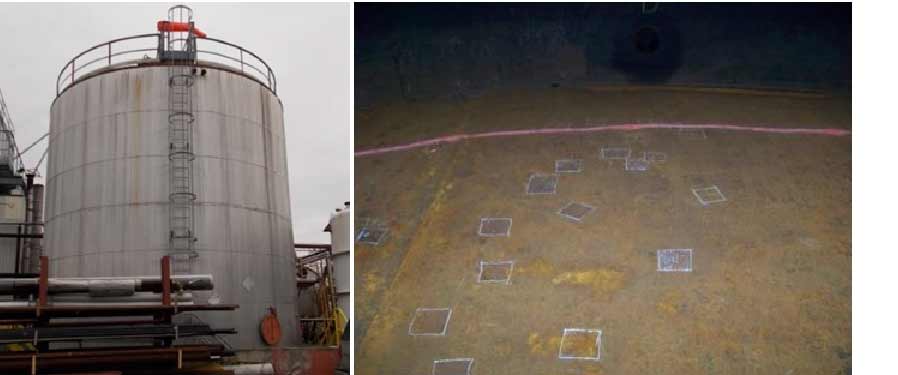
Making sure compliance with industry standards and laws is an additional considerable element of tank welding examination. Governing bodies mandate stringent guidelines for the construction and upkeep of tank, and comprehensive inspections aid organizations abide by these needs. Non-compliance can lead to severe fines, including fines and closures, even more emphasizing the demand for extensive inspection methods.
Moreover, storage tank welding examination plays an essential duty in maintaining operational effectiveness. In recap, the importance of storage tank welding assessment exists in its ability to protect public wellness, shield the environment, and guarantee conformity with governing structures.
Key Evaluation Methods
Reliable container welding assessment relies upon a selection of crucial strategies that make sure detailed analysis of weld top quality and architectural integrity. Among the most widespread techniques are aesthetic examination, ultrasonic screening, radiographic screening, and magnetic bit testing - Tank Welding Inspection. Each method offers unique benefits in analyzing various elements of the weld
Visual inspection functions as the initial line of defense, allowing assessors to recognize surface defects, abnormalities, or incongruities in the weld grain. Ultrasonic testing employs high-frequency acoustic waves to find interior flaws, such as splits or spaces, offering a comprehensive analysis of weld stability. This method is specifically efficient in spotting issues that might not be visible on the surface area.
Radiographic screening utilizes X-rays or gamma rays to generate photos of the welds, disclosing interior suspensions and giving a long-term record for future recommendation. This technique is very effective for critical applications where the danger of failure need to be reduced.
Last but not least, magnetic particle screening is employed to determine surface and near-surface flaws in ferromagnetic products. By applying electromagnetic fields and fine iron particles, assessors can determine gaps that could compromise the architectural integrity of the storage tank. With each other, these techniques form a robust framework for ensuring top notch welds in industrial applications.
Compliance With Safety And Security Standards

Regular assessments play a crucial duty in guaranteeing conformity by determining prospective failures or variances from recommended standards. Examiners are trained to review weld high quality, verify material requirements, and assess the overall structural stability of storage tanks. Their competence is crucial in ensuring that welding processes fulfill the required security requirements.
Moreover, conformity with safety standards not only safeguards employees but likewise safeguards the setting from potential threats such as leaks or catastrophic failures. Organizations that focus on safety and security conformity are better positioned to reduce threats, boost operational performance, and promote a society of security within their workforce. In summary, maintaining rigorous conformity with safety and security requirements is important for the successful operation of storage tank welding tasks in industrial settings.
Advantages of Routine Inspections
Routine assessments are essential to keeping the architectural stability and safety and security of bonded tanks. These inspections offer a systematic method to identifying potential problems or weak points in the welds, guaranteeing that any kind of concerns are resolved before they intensify right into substantial failings. By conducting routine evaluations, companies can detect corrosion, exhaustion, and visit this website various other kinds of wear and tear that may jeopardize storage tank efficiency.Moreover, consistent inspections add to compliance with sector regulations and criteria. Following these guidelines not just alleviates legal threats but likewise enhances the organization's track record for safety and reliability. Normal inspections promote a proactive safety culture, encouraging workers to identify and focus on the importance of devices integrity.
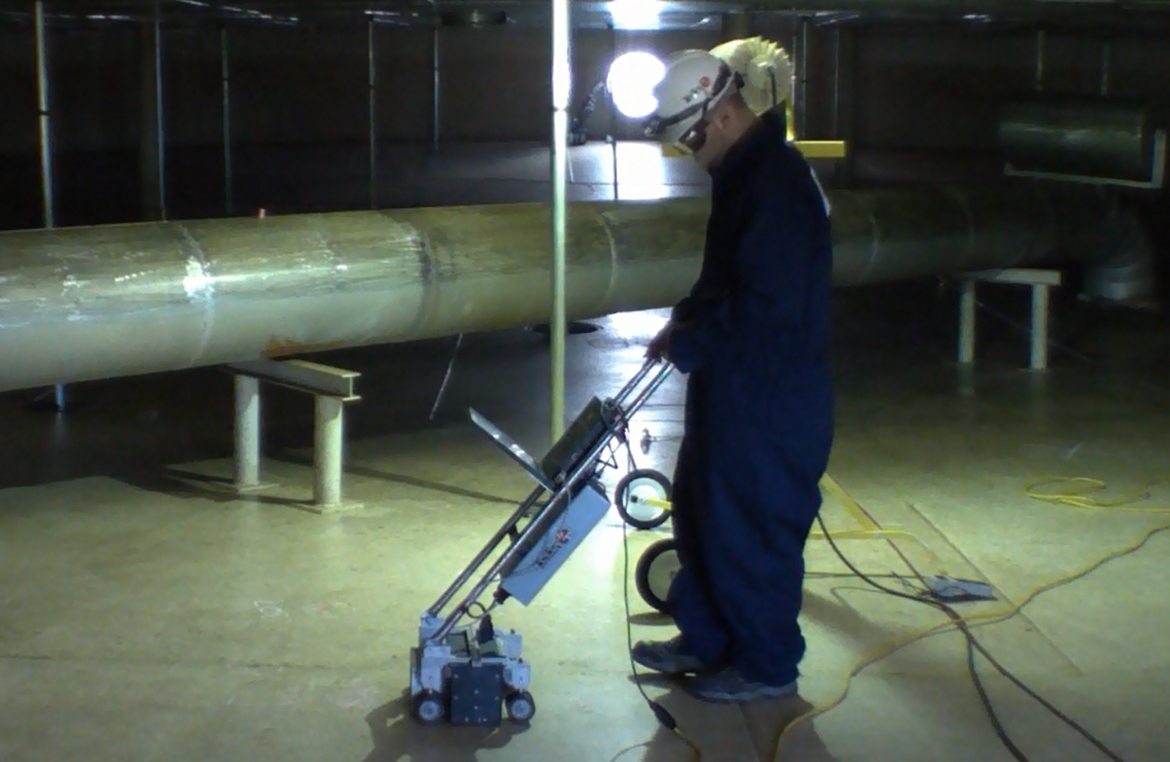
Study and Real-World Applications
Case studies and real-world applications illustrate the tangible influence of effective container welding inspection methods. Adhering to the execution of strenuous welding evaluation procedures, including visual and ultrasonic testing, the facility identified important problems in weld seams that might have led to disastrous failures.Similarly, a click for more info water treatment plant carried out a comprehensive assessment program for its container welding operations - Tank Welding Inspection. By incorporating non-destructive testing approaches, the plant had the ability to spot early indicators of deterioration and fatigue in weld joints. This prompt intervention prolonged the life-span of the storage tanks and made sure compliance with safety guidelines, hence securing public health and wellness
These case research studies highlight the relevance of regular and methodical storage tank welding see it here examinations. By prioritizing these techniques, markets can minimize risks, boost structural stability, and make certain compliance with safety and security standards, eventually bring about enhanced functional performance and decreased responsibilities.

Conclusion
In conclusion, tank welding inspection is an indispensable component of keeping architectural stability and security in industrial applications. Employing numerous examination strategies ensures early discovery of prospective defects, thus preventing catastrophic failings.Report this wiki page